case study --
Contactless Food Pickup Pod System Designed for High Foot Traffic Events
Chekt is changing the consumer dining experience for sports fans, restaurant go-ers, travelers, and more.
Chekt Product At A Glance
Chekt is an IoT Product built with Azure’s IoT technologies that allow hungry customers to mobile-order from food service stations and pick up their order from a pod, solving the problem of long lines and unnecessary human contact at restaurants, universities, airports, sports stadiums, and more.
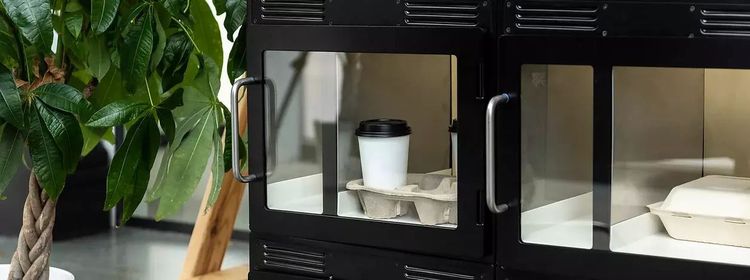
Ground Zero: Food Service Stations Shut Down by Covid Restrictions
Cargill, a B2B company that buys, sells and delivers food goods, recognized that Covid restrictions called for new food service solutions.
The Chekt product idea stemmed from the tensions of strict Covid dining and carry-out restrictions and their impact on the food industry.
A line-less food pickup pod experience was a new business venture for Cargill but aligned with their food-focused work. Through various connections with stadium suppliers, Cargill was confident that sports arenas would greatly respond to the convenience and safety of the Chekt “locker” pod system in place for its restaurants and food stands.
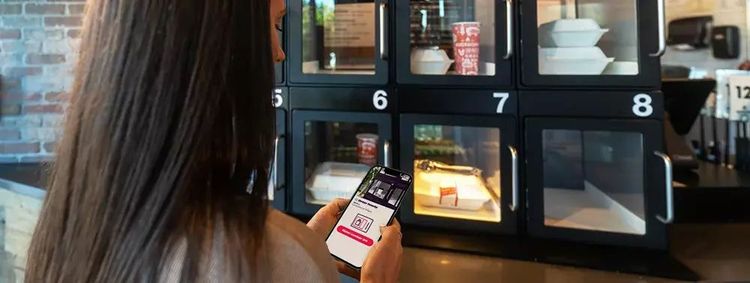
Square One: Product Partnership
In August 2020, five months into the Coronavirus pandemic, Cargill partnered with Monkeyjump Labs to create the Chekt product.
Monkeyjump Labs is a B2B software development agency that makes B2B and B2C software with expertise in building solutions for food & agriculture, education, manufacturing, entertainment industries, and more. Cargill is a B2B company that buys, sells, and delivers food goods. Cargill also provides data insights and analytics for its partners.
Before the Chekt engagement, Cargill and Monkeyjump Labs built another digital venture called Hot Take, a food-focused research platform connecting businesses seamlessly with their customer's food preferences.
Monkeyjump Labs’ proven expertise from prior product builds gave Cargill the confidence that MJL could deliver an expeditious and exemplary product. With the partnership established, the Chekt and MJL teams decided that the product would require bringing hardware to market with cloud-connected firmware. MJL brought expertise in firmware development to the project while hardware was primarily handled by another partner. As this was also one of the first digital solutions outside of Cargill infrastructure, they needed to navigate how to enable fast development and software deployment in the food service industry.
Dream Big: Product Ideation
What is the Chekt product, and how does it work?
Chekt is a secure food container that streamlines the food pickup process for food service station employees and the consumer ordering food.
How it works:
- A customer places an order.
- The restaurant fulfills it and loads it into a secure Chekt pod.
- The customer receives status updates and texts through SMS to unlock the pod and retrieve their order.
What problem does Chekt solve?
People want to avoid food ordering lines, human interaction, and wait times. With the Chekt contactless food pickup system, there are no crowds to navigate or lines for pickup like many mobile-order restaurants.
Benefits for restaurant owners:
- Employees can package food without taking time for in-person customer service issues, reducing labor costs.
- Owners gain visibility into the timeline of pickup for consumers and delivery drivers. The Chekt system adds traceability for orders within the scope of delivery, allowing restaurants to identify the time when delivery drivers pick up orders in case of an error/issue in delivery.
- A finished order is loaded into the bank of pods, reducing theft that can happen with a “grab and go” shelving unit that stands open to the public.
- Chekt integrates into existing POS software or ordering platforms – the software scales to any business's needs.
Benefit for customers:
- Food is easily accessible from the mobile app, from ordering to pickup.
- Food is placed in a temperature-controlled environment.
- The transmission of illness is reduced for the customer as they do not wait in line or interact with staff.
The Technology:
Azure - cloud service provider:
Azure IoT + Sphere
Azure Functions
Azure Cosmos DB
Embedded Linux Devices
Get to Work: Product Development Phases
MVP-to-Scale process:
Monkeyjump Labs used their MVP-to-Scale process to build a rapid MVP that users could interact with and react to. The MVP-to-Scale process is successful because it prioritizes constructive work over perfect planning, leans on the expertise of building products to make the right decisions, and requires consistent (weekly or bi-weekly) milestones to showcase progress and iterate on ideas.
MVP-to-Scale happened in three stages:
What software/technology runs the product while in use?
- Monkeyjump Labs leveraged .NET Core for the web APIs, middleware, and other server-side applications.
- React was the framework for web application UI.
- Web sockets to push updates to the interface so we can see changes.
- Contacted users via SMS and the embedded software on the devices (pods)
- C++ Firmware and Azure Sphere for native components
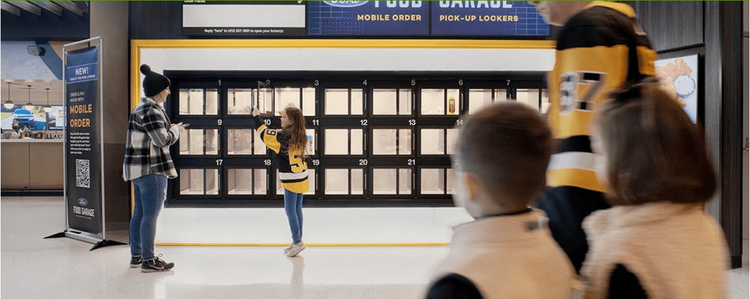
In the End: Product Results and Benefits
In January 2023, the Chekt system was an Innovation Awards Honoree at CES.
In all stages of development, Monkeyjump Labs brought the software expertise on “how to” functionally accomplish each task and how to scale the application.
Together, Cargill, MJL, and other partners celebrate the traction Chekt has experienced in the market, and subsequent growth in product and use case.
MJL enjoyed being a part of the success of the Chekt contactless food system and believes that Chekt will impact the food service industry and the people it serves in a valuable way in the years to come.